1. 加工难点分析
图1所示为某柴油机圆盘零件示意图,年需求量35 000件,材质为10钢,料厚t=5mm,外形φ(219 ±0.1)mm, 内孔,成形高度(10.5±0.2)mm,断面光亮带达75%以上。因产品对尺寸、断面质量要求较高,综合考虑,采用落料→成形→精冲的工艺。经分析,该产品主要的加工难点是内孔φ的尺寸难以保证,只能靠后续加工,原因为:①根据精冲技术规程VDI3345及Schmid资料,料厚t=5mm、内形尺寸φ135mm产品的公差应为IT8级,即63μm,而产品要求为40μm,远小于可满足的范围。②孔φ135mm与腰圆孔间的壁厚为3.5mm,仅为料厚的70%,此处材料稳定性差,会影响内孔φ135mm尺寸。
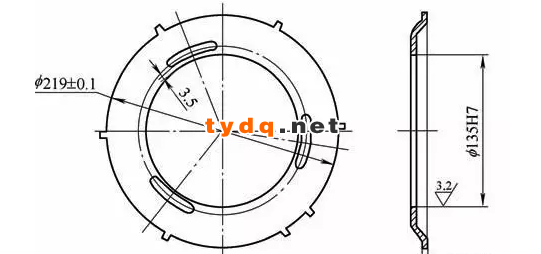
此产品批量大、精度要求高,考虑到经济性及产品质量,采用精冲时留适量余量、后续数控车到尺寸的加工方法。
2. 初始加工方案
按照常规方法, 如图2 所示,数控车时夹紧零件外圆。实际生产中发现,产品加工完从机床上取下后,内孔尺寸有变化,且腰圆处尺寸与非腰圆处尺寸也不同,相差达0.03mm以上,难以满足产品要求。分析后认为:
夹紧产品外圆时会对产品施加径向力,使产品发生径向变形;腰圆处壁厚明显薄于其他部位,在切削力的作用下会产生更大的变形。切削完成后及产品取出时外力消除,产生回弹,使内孔尺寸发生变化。针对以上特点,我们对装夹方式作出了改进。
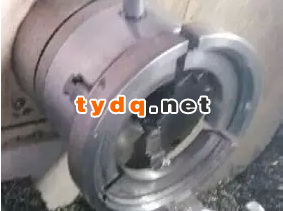
图2 常规装夹示意图
3. 改进方案
设计专用夹具如图3所示,使用3个快速压紧器压紧零件端面,无径向力且相对传统压块压紧操作方便、节省时间,易于控制夹紧力的大小;在零件腰圆中靠近内孔处设置6个定位钉和一个防转钉,增加零件刚性,防止零件转动。为保证批量生产时产品尺寸的稳定性,需校正夹具端面与机床主轴的垂直度0.02mm以内,定位钉侧面与机床主轴的同轴度0.02mm以内,定位钉侧面与产品配合间隙0~0.005mm。
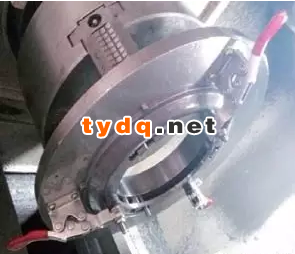
图3 改进后的装夹示意图
经批量生产验证,产品内孔尺寸合格率可达100%,唯一不足的是校正夹具垂直度对操作工的技能要求很高,浪费了大量工时,有待进一步优化。
4. 工艺优化
将定位钉尺寸加大,留适量余量在夹具端面校正后数控车,直至与产品的配合满足要求,这一方法减少了对定位钉的校正,且对定位钉位置、原始尺寸无太高要求,仅需每批更换定位钉即可。
5. 结语
经过一系列改进,圆满解决了圆盘零件高精度内孔尺寸这一瓶颈问题,且满足大批量生产的要求,同时为其他类似产品的制造提供了一种可行的思路。
更多产品信息请关注铁艺大全网:www.tydq.net,转载请注明出处。