乌兹别克斯坦机车采用轮盘制动形式。该轮盘制动装置代替了闸瓦对车轮踏面的摩擦,可减少车轮的磨耗,延长车轮的使用寿命,保证运行安全。因此,轮对驱动部分与其他机车的轮对有所差别,在其他机车制造经验的基础上,对乌车车轮加工工序进行了改进与完善,从而制造出符合设计要求的乌车车轮。
1.工艺难点分析
乌兹别克斯坦机车采用轮盘制动方式,制动盘通过扁销和螺栓联接,将其安装在车轮两侧幅板位置,其结构如图1所示。因此设计对车轮制动盘安装面、制动盘安装的销孔6×φ28+0.033 0mm、传力销孔6×φ54 +0.033 0mm的表面质量和形位公差要求很高;乌车采用齿轮空心轴传动装置联接电动机与轮对,主动车轮上幅板面有6个传力销孔,动力通过传力销传递到轮对,从而牵引机车运行。传力销孔的位置度在很大程度上影响到动力传递的均衡性,因此,销孔的尺寸及形位公差要求很高。
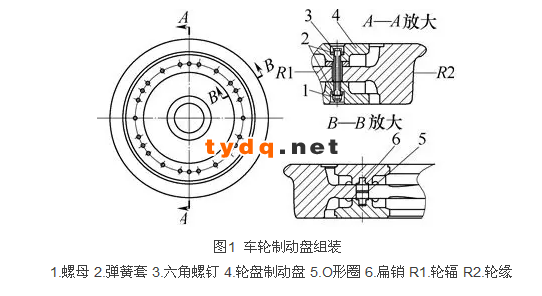
2.孔加工工艺方案的确定
(1)加工工艺分析。通过对乌车车轮进行工艺分析,加工工艺重点与难点如下:
6个φ54+0.033 0mm传力销安装孔的加工,要求加工精度达到H7级精度,且需要保证传力销安装孔φ54+0.033 0mm相对基准A的位置度误差不大于φ0.08mm。
6个扁销安装孔φ28+0.052 0mm的加工,且需要保证孔φ28+0.052 0mm相对基准A的位置度误差不大于φ0.2mm。
车轮装夹定位所需工装要保证车轮平行度0.02mm的要求,且要方便车轮的装夹和适合刀具加工时的移动。
乌车车轮滚动圆φ1 256+1 0mm,比其他机车车轮轮径大,根据其结构特点,设计专用乌车主动轮的销孔和制动盘螺栓安装孔加工工装,通过对乌车中心孔及轮辋面的一次装夹定位进行加工。为了保证其形位公差及精度要求,综合考虑加工方法与工件技术要求等因素,编制了如下加工工序:校正φ54+0.033 0mm孔→半精镗→精镗→钻φ4mm中心孔→钻φ28+0.052 0mm底孔→扩孔→铰孔→钻φ4mm中心孔→钻φ20+0.2 0mm底孔→扩孔→镗孔。
(2)设备和工装。设备:THK46100卧式加工中心,数控系统:FANUC 0MC,工作行程:X=2 000mm、Y=1 200mm、Z=1 350mm,定位精度:0.001/300mm,工作台规格:1 000mm×1 000mm,工装:乌兹别克斯坦机车车轮镗孔夹具。
为了解决上述工艺难点,以及进一步提高生产效率特设计为L形专用工装,利用加工中心的高精度、高效、高可靠性等特点,对乌车主动车轮进行加工,使夹具在保证产品质量的同时,尽可能提高工作效率并降低操作者的劳动强度。该工装采用内孔及靠面定位方式,其定位靠面平面度要求为0.02~0.04mm,与工作台定位面垂直度要求为0.02~0.05mm。中心定位心轴起承重作用,采用圆柱轴承弹性联接,圆柱可相对于支撑点转动,可有效地防止车轮在装夹过程中的内孔擦伤。
(3)车轮装夹及调试。安装时用百分表校正夹具4个定位块所处平面的平行度、垂直度在0.02mm以内,将车轮内侧面向外装夹,如图4所示,采用两个心轴在车轮内孔定位并支撑,然后通过4个压板压紧车轮内侧辋面,保证外侧辋面与夹具4个定位面贴平,夹紧后校正车轮内侧辋面的平行度、垂直度,同时用百分表校正车轮内孔,校正误差在0.02mm以内,并以该点作为工件的编程零点,从而解决了传力销安装孔φ54+0.03 0mm相对基准孔轴线0.08mm的位置度要求。
在夹紧车轮内侧面后由于工装设计为L形,后面压紧点比较少,工装在单独安装时打表校正垂直度误差在0.02mm,工件装夹上以后打表校正内侧辋面上下垂直度为0.2mm,后经分析为车轮本身质量达733㎏,夹紧后车轮有向前倾斜的趋势,这样垂直度超差会直接影响6个φ28+0.052 0mm销孔和6个φ54+0.03 0mm传力销孔相对于基准孔的位置度公差,造成加工产品质量不合格。为了避免垂直度带来的影响,通过摸索和试验,使工装安装时在不影响刀具方便加工的情况下,尽量靠近工作台中心部位并在工装后端上加一个配重块,如图4所示。经受力分析计算,配重块确定为400㎏的铁块较为合适。此时车轮内侧辋面的平行度、垂直度校正误差控制在0.03mm以内,从而更好地保证各孔位的位置公差。
(4)加工步骤。①将工件吊上定位工装,并使一左方φ54mm孔垂直于90°夹紧轮辋内侧面;用磁座式百分表校正车轮内孔及辋面,校正误差在0.02mm以内,并以内孔中心作为程序零点X、Y座标零点。②按加工程序(旋转坐标系、极坐标程序),用双刃镗刀试镗6个φ54+0.03 0mm孔,深0.5mm,保证6个φ54+0.03 0mm孔周边均有加工余量,否则就旋转X、Y坐标系至合理位置。③用双刃镗刀粗镗6个φ54+0.03 0mm孔至6个φ53.5mm;用微调镗刀精镗6个φ54+0.03 0mm孔至尺寸、表面粗糙度值Ra=1.6μm;倒6个3mm×10°导向锥(刀具:导向锥成型刀);用A4中心钻头钻6个φ28H8和18个φ20mm各孔中心孔;用φ19mm钻头将18个φ20+0.2 0mm孔钻成φ19mm;用φ7mm钻头将6个φ28H8孔钻成φ27mm;用φ27.75mm扩孔钻扩6个φ28mm孔至φ27.75+0.2 0mm;用铰刀铰6个φ28H8、表面粗糙度值Ra=1.6μm;用φ19N21扩孔钻扩18个φ20mm孔至φ19.75+0.1 0mm;用铰刀铰6个φ20+0.2 0mm、表面粗糙度值Ra =3.2μm;用倒角刀倒φ28mm和φ20mm各孔内侧45°×1.5mm。
通过使用上述刀具和工艺方法,使该产品加工的尺寸精度、表面粗糙度和位置度达到设计要求,但由于该加工工序繁琐,刀具种类较多,导致了加工效率低下,与此同时还发现生产过程中,所用的φ19mm钻头和φ27mm钻头在加工时,刀具磨损较大、钻削时有异音、钻削出的孔变大,使后续无法加工或表面粗糙度值无法达到图样要求。为此对问题进行了深入分析和研究,通过多次试验加工,发现刀具磨损较大和加工时有异音的主要原因有两点:钻头的手工刃磨角度不合适;车轮材质较硬,切削参数未合理选择。
为解决上述问题,通过反复的试验和摸索,最终确定钻尖合适的角度为108°~115°,在这个角度范围内,选择合理的切削参数就能避免钻头断裂、烧死和有异音的现象,通过一段时间的加工,虽然解决上述问题,但利用麻花钻头加工乌车车轮生产效率较低,为了适应公司快速发展的要求,保证生产进程的顺利进行,必须对现有的加工工艺进行优化。通过查阅相关的加工资料发现U钻加工孔的效率较高,对其进行研究分析后,最终采用U钻代替麻花钻头加工乌车车轮6个φ28mm销孔和18个φ20+0.2 0mm螺栓孔。
(5)加工工艺优化——U钻的运用。现用加工工序繁琐,刀具种类繁多,麻花钻头刃口修磨的难度较大,每次刃磨的标准无法统一,再加上考虑加工设备、工件材质及工件需要达到的尺寸要求等多方面因素,特提出优化钻削加工工艺,实施高速切削的工艺方式,缩短加工时间,提高加工稳定性,并使用新型的钻削刀具——可转位螺旋槽直槽浅孔钻头,即选择合适规格的U钻和数控车床来实现一次加工成形的切削加工,可以减少使用刀具、改善工件质量。以CoroDrill880 U钻为例(见图5),其型号: CoroDrill(R) 880 3×Dc,钻头直径12~43.99mm。
CoroDrill880 U钻,应用了阶进技术(StepTechnology)。阶进技术提供了优良的切削力平衡,显著地提高了生产率和孔质量。钻头有独特形状的中心刀片,使用了台阶技术,以光滑的入口切入工件,很好地平衡了切削力,使进给量提高100%,从而将成本降低一半。
U钻特点:效率翻番;更小的孔公差,提高了表面质量;真正的4切削刃,并具有Wiper(修光刃)效应;进行了全新表面处理的更坚固钻体,能够承受更高的进给;Wiper(修光刃)槽形,保证了最佳的表面质量;加工直径范围从12mm扩展到63mm。
随着高速加工应用范围的扩大,对新型刀具材料的研究、刀具结构的改进、数控刀具路径新策略的产生和切削条件的改善也有所提高。而且,切削过程的计算机辅助摸拟也出现了,这项技术对预测刀具温度和应力、延长刀具使用寿命很有意义。很显然,随着各项新技术的不断成熟和综合运用,以高效率、高精度和高表面质量为基本特征的高速切削加工技术的应用已经越来越广泛,并且取得了重大的技术经济效益。
程序说明:程序的编制适当地使用了极坐标、坐标系旋转、钻孔固定循环和镗孔固定循环,使用了上述程序指令,大大减少了程序的编制量,便于检查及避免错误,使整个程序紧凑有序、条理清晰,同时经过反复调试验证加工工艺、合理选择切削参数,最终加工出满足技术要求、符合质量标准的合格产品。钻头、U钻使用对比情况如附表所示。
钻头、U钻使用对比情况表
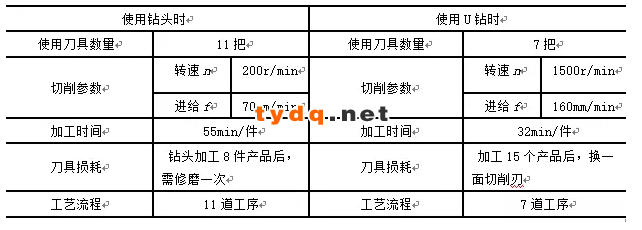
效率提升情况简介:通过附表所示,通过使用前后对比,改进后加工效率大幅度提升。
3.结语
通过合理地使用机床数控系统指令,很好地解决了刀具的定位和使用寿命;而专用工装的使用,能充分利用加工中心的高精度、高可靠性等特点,保证了乌车车轮孔加工的形位公差、尺寸精度和表面质量,通过使用U钻,优化加工工艺、合理选择切削参数,降低了劳动强度,提高了加工效率。
更多产品信息请关注铁艺大全网:www.tydq.net,转载请注明出处。